lumberjack
Young man on the go
I've replaced the 2 section pump with the single section pump and have it workingish, but I do have a couple things to figure out.
Firstly, the GPS said it topped out at 5.3mph, which is flippin great by me.
Here's the factory schematics:
Here's what I tried:
Disconnected line 26 from the dump valve (fitting 19), and connected it straight to the pump. I thought this would kill two birds, one, it'd bypass the silly safety chit (dump valve), and it'd get the fluid straight to the valves in the most direct manner. That didn't work for reasons unknown. The engine stalled, obviously the fluid is working against itself somewhere.
So, what I did was return line 26 to fitting 19, connect fitting 33 (right) to pump while capping the other 33 (left).
Now the fluid is going back through the dump valve and the circuit breaker valve (13).
Before I push the safety interlock button (for the main hydraulics), the engine runs/idles fine. There's no undue load on the engine like the pump is having to work against inline restrictions going from its outlet to through the circuit breaker and dump valve to tank. When I push the interlock button, closing the dump valve and running fluid through hose 26, the engine sounds like it has a slight load against it. If I try to feather a control, the loading increase. If I run the controls wide open, there is the initial increase in load which then decreases as the machine gets to speed.
All the hoses are 3/8", and it happens if the engine is at idle, WOT, or anywhere in between. That lets me know it's not from too much flow going through the valves, as at idle the pump puts out less fluid than the original at WOT.
I'm miffed why I couldn't run hose 26 straight to the pump, so I'm guessing it has something to do with the over center valve in both configurations.
I'll make a video to better illustrate how the machine is acting.
Another question, does anyone know the in tank strainer's filter number?
Firstly, the GPS said it topped out at 5.3mph, which is flippin great by me.
Here's the factory schematics:
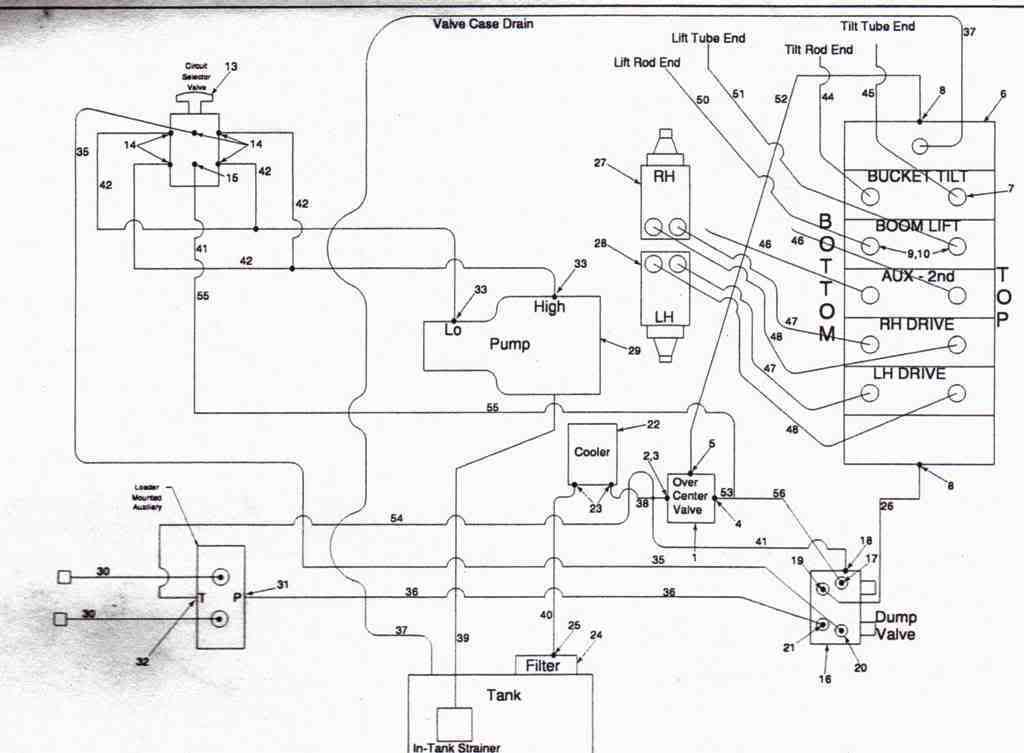
Here's what I tried:
Disconnected line 26 from the dump valve (fitting 19), and connected it straight to the pump. I thought this would kill two birds, one, it'd bypass the silly safety chit (dump valve), and it'd get the fluid straight to the valves in the most direct manner. That didn't work for reasons unknown. The engine stalled, obviously the fluid is working against itself somewhere.
So, what I did was return line 26 to fitting 19, connect fitting 33 (right) to pump while capping the other 33 (left).
Now the fluid is going back through the dump valve and the circuit breaker valve (13).
Before I push the safety interlock button (for the main hydraulics), the engine runs/idles fine. There's no undue load on the engine like the pump is having to work against inline restrictions going from its outlet to through the circuit breaker and dump valve to tank. When I push the interlock button, closing the dump valve and running fluid through hose 26, the engine sounds like it has a slight load against it. If I try to feather a control, the loading increase. If I run the controls wide open, there is the initial increase in load which then decreases as the machine gets to speed.
All the hoses are 3/8", and it happens if the engine is at idle, WOT, or anywhere in between. That lets me know it's not from too much flow going through the valves, as at idle the pump puts out less fluid than the original at WOT.
I'm miffed why I couldn't run hose 26 straight to the pump, so I'm guessing it has something to do with the over center valve in both configurations.
I'll make a video to better illustrate how the machine is acting.
Another question, does anyone know the in tank strainer's filter number?