2 years ago I was given a large beech burl by a forwarder driver.
I was going to make a bowl for him out of it, but ended up giving all the stuff I cut out of the middle with my centersaver and the off cuts to members of the Danish woodturning forum.
Here is what came out of that:
The burl in it's raw form:.
The bowl I made from it:
I was going to make a bowl for him out of it, but ended up giving all the stuff I cut out of the middle with my centersaver and the off cuts to members of the Danish woodturning forum.
Here is what came out of that:
The burl in it's raw form:.
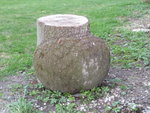
The bowl I made from it:
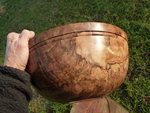
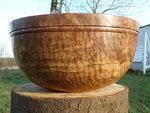