bonner1040
Nick from Ohio
So I got a picture from my boss and it reminded me of one thing that bothered me about the job:
I was cutting a notch in a fairly well sized spar (Burnham...i didn't call it big
) I was running the 066 with a 28" bar which was the biggest i had available. The back of the notch ended up more than twice the length of the bar because as the saw came across on the bottom cut the operator rotated the saw from right to left setting the depth by burying the bar. (The bottom cut was made by the 'boss/estimator/guy' and I took over after it was clear he was a little out of his comfort zone.)
I didn't have any problems lining the cuts up and after placing the top cut and piecing the notch into thirds I smashed the pieces out with a sledge...
As you can see above I ended up with some 'remainder' in the middle, ultimately it was held on by mere slivers, but I couldn't get it out whatever I tried... Every time I tried to get the saw in there it just kicked and I gave up trying.
In the end I just dropped the stick because we were in a field and it didn't REALLY matter where it fell. I try to do everything the right way if only to learn and it bothers me a bit that I couldn't get the notch clean. It fell right on target and the stuff left in there didn't make the hinge break early or anything.
Looking at the picture, there were cuts into the 'remainder' on top and bottom parallel with the inside of the notch. It was really held on just by the back where the top and bottom meet. FWIW I tried smashing it out obviously.
Any tips?
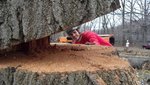
I was cutting a notch in a fairly well sized spar (Burnham...i didn't call it big

I didn't have any problems lining the cuts up and after placing the top cut and piecing the notch into thirds I smashed the pieces out with a sledge...
As you can see above I ended up with some 'remainder' in the middle, ultimately it was held on by mere slivers, but I couldn't get it out whatever I tried... Every time I tried to get the saw in there it just kicked and I gave up trying.
In the end I just dropped the stick because we were in a field and it didn't REALLY matter where it fell. I try to do everything the right way if only to learn and it bothers me a bit that I couldn't get the notch clean. It fell right on target and the stuff left in there didn't make the hinge break early or anything.
Looking at the picture, there were cuts into the 'remainder' on top and bottom parallel with the inside of the notch. It was really held on just by the back where the top and bottom meet. FWIW I tried smashing it out obviously.
Any tips?